How the IIOT optimizes production flow
Link to this heading # How the IIOT optimizes production flow
What is it about the Industrial Internet of Things that’s so special? The fact that it’s a technological revolution? Or that it brings us closer to the future? Or that it builds a world in which machines can carry out all the tasks humans cannot?
All three are good, but equipment that can make our companies more efficient and bring the global economy to a higher pedestal by performing tasks humans are too slow to accomplish is quite a feat.
SENSORS ARE MORE EFFICIENT THAN HUMANS.
Humans have certainly proven useful in the world of manufacturing. They run the floors, oversee production lines, and ensure items are delivered in a timely manner. For the most part, humans know their place and perform their duties with general ease and confidence.
But that doesn’t mean humans are capable of everything. With today’s growing technology and the power of the IIoT, machines are now inter-connected with each other, and produce data at much faster speeds. This information is ultimately used to garner information regarding operations (i.e. what issues require attention, what parts aren’t working to their full capacities, etc.) Executives and factory managers can then oversee production and stay on top of all their daily business.
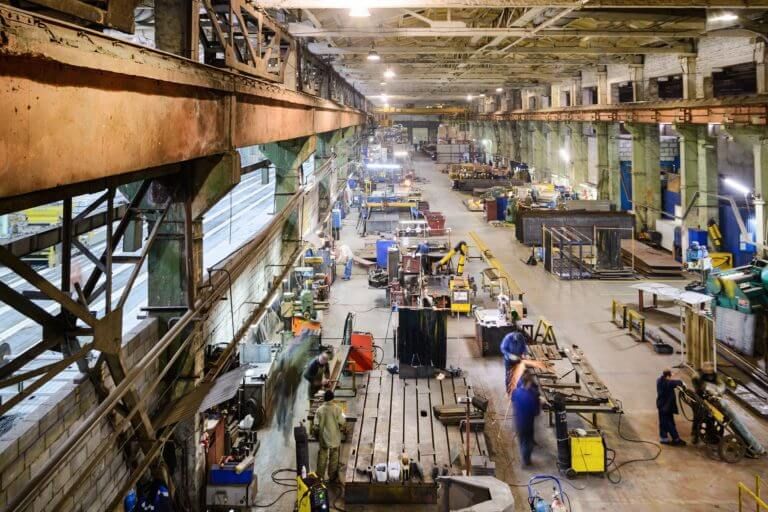
Data is produced too fast for humans to gather themselves. Our minds and hands can only work up to a certain point before they start to get tired. If 50 employees were working in-sync to collect data from a single sensor, it would still take too long. We couldn’t decipher in one day what sensors can in mere hours. They’re faster, stronger and more efficient. Period.
Link to this heading # THIS IS A GOOD THING!
But this isn’t necessarily something to cry about. As human beings, it’s important to know our weaknesses, and understand when it’s time to step aside and let the “big boys” jump in. The IIoT optimizes production lines, and can increase their efficiency through careful sensor placement and monitoring. For example, some sensors may be monitoring rising temperatures in factory machines and see that these temperatures are somehow decreasing efficiency (or vice versa).
Intelligent sensors and lower-cost sensors ultimately work together with wireless connectivity and big data processing tools to make the process of data collection cheaper and easier than it has ever been. Granted a manufacturer owns equipment or machinery “designed to operate within a certain temperature, vibration or stress range,” sensors can ultimately be used to monitor factory activity on a regular basis should anything move out of range. This can initially tackle and prevent malfunctions before they become too heavy or difficult to handle.
Link to this heading # ADDITIONAL BONUS.
The real clincher in all this is how sensors allow machines to communicate with each other. “Digital conversations” are what allow machines to share and exchange data, and inform one another about where issues are stemming from. Executives then see this data projected onto a central source and decipher or diagnose which areas require immediate attention. They can schedule maintenance from there, make decisions with ease, and work to ensure all equipment remains in tip-top shape.
Link to this heading # CONCLUSION.
As with any company, we’ve learned that communication is key. It would appear this rule applies to both humans and machinery alike, and for operations to work and be effective, the exchange of information in multiple capacities is indeed necessary. Without this exchange, humans and sensors cannot get the data they need to make informed decisions about what to replace, repair, or keep as is. This constant flow of communication is what every factory or global enterprise needs to stay afloat, make improvements, and grow with time, and the IIoT is undoubtedly readying the world for a heightened sense of production and economic change.